 |
 |
 |
 |
 |
|
|
 |
|
 |
|
 |
|
|
|
|
Infinity Ammonia Standard Set

Title Slide

Pharma MiniLab

Residence time measurements

Relevant Process Parameters

Investigating process

Streamline Drug Development

Comprehensive Compounding
|
|
Pharma Hot Melt Extrusion System &
Granulator
Pharma 11 Twin screw Extruder
- Perform material and labor effective extrusion with Thermo Scientific Pharma 11 Twin screw Extruder, which requires only a small amount of active pharmaceutical ingredient, operating at throughput levels as low as 20g/h.
The parallel 11mm twin screws and compact design of the Pharma 11 Twin screw Extruder is fully scalable with the Thermo Scientific stand alone pharmaceutical compounding systems.
Together, you can obtain process relevant results or even perform small scale production.
If you need a complete extrusion solution, a wide range of accessories are available for the Pharma 11 Twin screw Exturder, including volumetric and garvimetric, feeders, a conveyor belt and a pelletizer.
The Pharma 11 Twin-screw Extruder Features:
- Uses smaller material quantities for faster, cost-effective development
- Converts easily from hot melt extrusion (HME) to twin screw granulation (TSG) applications
- Operates at throughput ranges from 20g/h up to 2.5kg/h
- Processing length: L/D ratio 40:1
- Screw elements and barrel design scale geometrically across the all Thermo Scientific Pharma Extruders and allow easy process scale-up
- Easy-to-operate with user-friendly, intuitive touch screen with integrated feeder control
- Maximize lab space with small footprint machine
- Perfect for glove box or isolator applications with removable touch screen
- All material contact parts are easily removable
- Documentation of extrusion parameters and suitable for process analytical technology (PAT)
- GMP-compliant, full validation available: FAT, SAT, IQ/OQ
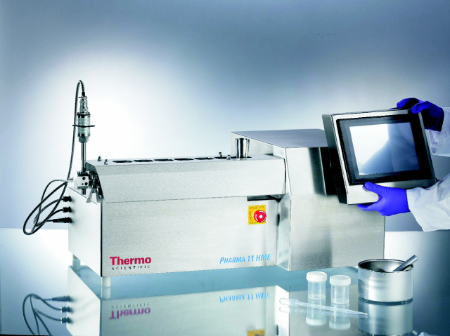
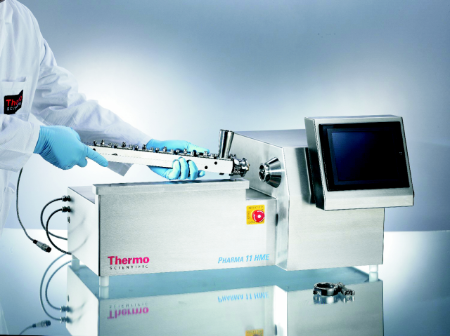
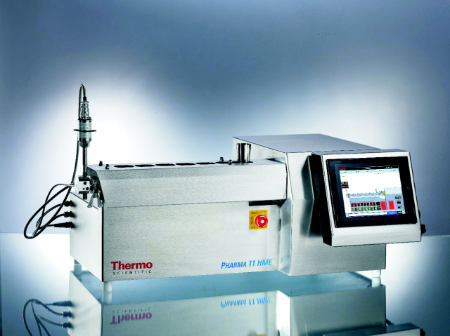
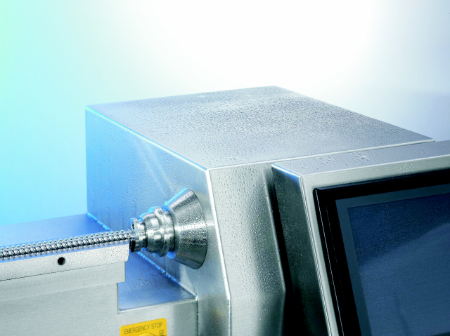
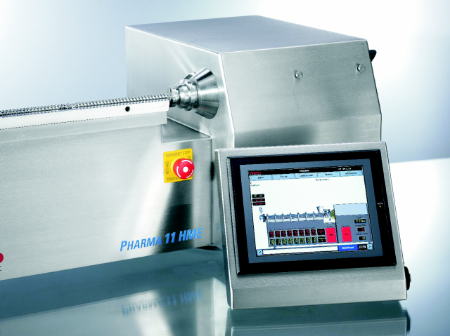
|
|
|
|
|
|
 |
|
|
|
|
Specification_Sheet_-_Pharma_16_Twin-Screw_Extruder

Application_Note_-_Investigating_Process

|
|
Pharma 16 Twin-Screw Extruder
- Thermo Scientific¢â Pharma 16 Twin-Screw Extruder·Î ¾àǰ Á¦Á¦¹ýÀ» ½Å¼ÓÈ÷ °³¹ßÇÏ°í ¿¬¼Ó °¡°ø ¹æ½ÄÀ» ¼öÁ¤ÇØ º¸½Ê½Ã¿À. Pharma 16 Twin-Screw Extruder´Â ¿¬¼Ó °í¿Â ¿ëÀ¶ ¾ÐÃâ(HME)°ú ½À½Ä °ú¸³È(TSG) ¹æ½Ä »çÀ̸¦ ½±°Ô ÀüȯÇÒ ¼ö ÀÖ½À´Ï´Ù. ¹îÄ¡ °øÁ¤º¸´Ù ´õ ÀûÀº ½Ã°£°ú ³ë·ÂÀ¸·Î ¾à¹° °øÁ¤ÀÇ °³¹ß º¯¼ö¸¦ ÃÖÀûÈÇϰí, °í°¡ÀÇ API ¹× ÷°¡Á¦ »ç¿ëÀ» ÃÖ¼ÒÈÇÏ¿© ´õ Å« ¿ë·®ÀÇ Thermo Scientific¢â ¾ÐÃâ±â·Î È®ÀåÇÒ ¼ö ÀÖ½À´Ï´Ù.
Pharma 16 Twin-Screw Extruder´Â Á¦¾à »ê¾÷¿¡¼ ¿¬±¸, °³¹ß »ý»ê¿¡ »ç¿ëµÇ´Â ½Ã¹ü ±Ô¸ðÀÇ ¿¬¼Ó HME ¶Ç´Â TSG 󸮿¡ ÀûÇÕÇÕ´Ï´Ù. ±â¾÷Àº °íÇü¿ë ¿¬¼Ó °øÁ¤À» °³¹ßÇÏ¿© Àϰý °øÁ¤¿¡ ºñÇØ ½ÃÀå¿¡ ´õ ¸¹Àº ¾çÀÇ Á¦Ç°À» ´õ ºü¸£°Ô Ãâ½ÃÇÒ ¼ö ÀÖ½À´Ï´Ù. Pharma 16 Twin-Screw Extruder¸¦ »ç¿ëÇÏ¸é ¾à¹° Àü´Þ ¹× Á¶Á¦¸¦ À§ÇÑ ¾à¹° Á¦Á¦¿¡ ÀÖ¾î ½Ã¹ü ±Ô¸ðÀÇ °øÁ¤ Á¶°ÇÀÌ ¹ÌÄ¡´Â ¿µÇâÀ» ½±°Ô ¿¬±¸ÇÒ ¼ö ÀÖ½À´Ï´Ù.
Pharma 16 Twin-Screw ExtruderÀÇ Æ¯Â¡:
- ÅõÀοø(2-in-1) ÇÁ·Î¼¼½º ¼³°è - ½¬¿î ¼¼Ã´°ú HME¿¡¼ TSG·ÎÀÇ °øÁ¤ ÀüȯÀ» À§ÇØ ºÎǰÀ» ºü¸£°Ô ºÐÇØÇÒ ¼ö ÀÖ½À´Ï´Ù.
- °£´ÜÇÑ ¿¬¼Ó °øÁ¤ ÅëÇÕ - Ç÷¡±×¾ØÇ÷¹ÀÌ ±â´É°ú ¾÷½ºÆ®¸² ¹× ´Ù¿î½ºÆ®¸² ó¸® Àåºñ(°ø±Þ±â, ³Ã°¢ ·Ñ, Æç¸®Å¸ÀÌÀú, °ÇÁ¶±â µî)·Î »ý»ê ¶óÀÎ ¼³°è¸¦ °£¼ÒÈÇÕ´Ï´Ù.
- ÃÖÀûÈ ½Ã°£, ºñ¿ë, ³ë·Â °¨Ãà - Áö¿À¸ÞÆ®¸®°¡ À¯»çÇϱ⠶§¹®¿¡ °í°¡ÀÇ ±¸¼º¿ä¼Ò¸¦ ÃÖ¼Ò·Î »ç¿ëÇÏ¿© ¾ÐÃâ±â ó¸® º¯¼ö¸¦ ´ë±Ô¸ð Thermo Scientific ¾ÐÃâ±â·Î È®ÀåÇÒ ¼ö ÀÖ½À´Ï´Ù.
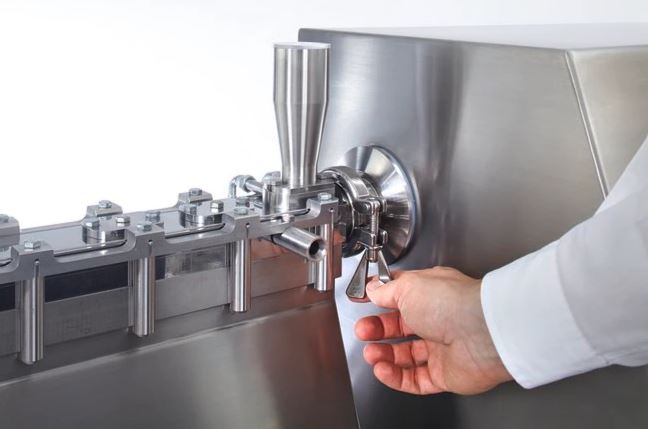
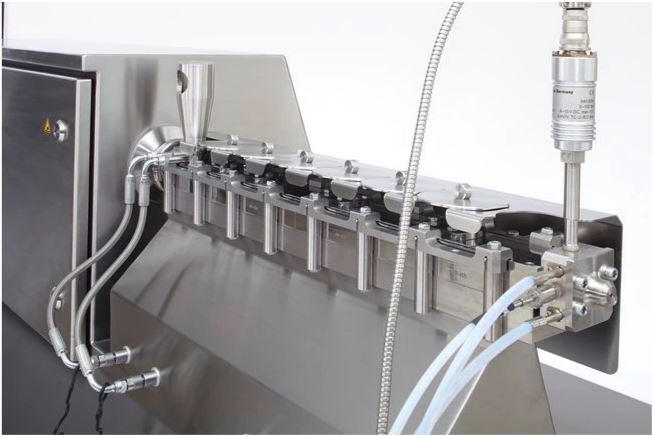
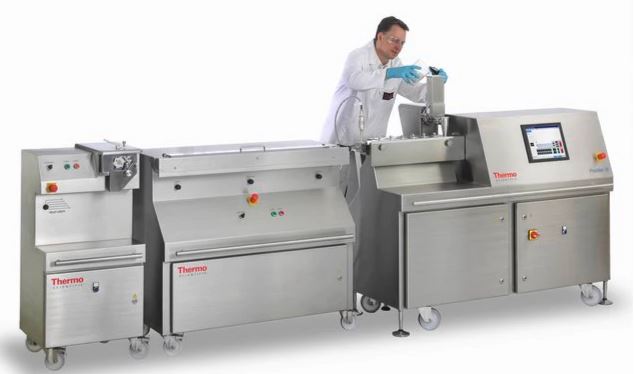
|
|
|
|
|
 |
Specification_Sheet_-_Pharma_24_Twin-Screw_Extruder

|
|
Pharma 24 Twin-Screw Extruder - The Thermo Scientific¢â Pharma 24 Twin-Screw Extruder, with avaialble HME and Twin-Screw Granulation (TSG) Application Sets, is ideal for continuous processing in research, development or production in the pharmaceutical industry. The Pharma 24 extruder drives reduced clean room area, consistent and controllable processing, reduced product changeover time, on-demand production, minimized scale-up risk and reliable cleaning. It is suitable for process analytical technology (PAT).
The Pharma 24 Twin-Screw Extruder features:
- A small footprint to take up less space in clean rooms
- Continuous operation which consumes fewer utilities than traditional batch processes
- High free volume screw design
- A small process inventory
- Lower ingredient consumption which reduces handling and operator exposure
- Segmented screws and barrel
- Removable screws and liners
PAT Compatibility: PAT can be applied to your process to monitor parts of theprocess such as homogeneity of mixing or moisture content to assure required product quality. The Pharma 24 Extruder can be used with a range of PAT instruments such as Thermo Scientific¢â FT-NIR system.
Options: We offer a full range of GMP compliant ancillaries which are matched to the extruder performance. This downstream equipment can be integrated into the extruder control system.
For TSG configurations: available ancillaries include volumetric or gravimetric dosing feeders and liquid injection pumps.
In addition, self-contained units of either configuration can be operated with recirculating chillers to reduce water consumption.
TSG configuration recommended for:
- Wet granulation
- Dry/melt granulation
For HME configurations: available ancillaries include volumetric or gravimetric dosing feeders, air cooled conveyors for product cooling, strand and face-cut pelletizers to make pellets, or chill roll/flaker units for rapid product cooling and flaking.
HME configuration recommended for:
- Solubility enhancement
- Modified release
- Co-extrusion
- Drug delivery systems
- Biomedical products
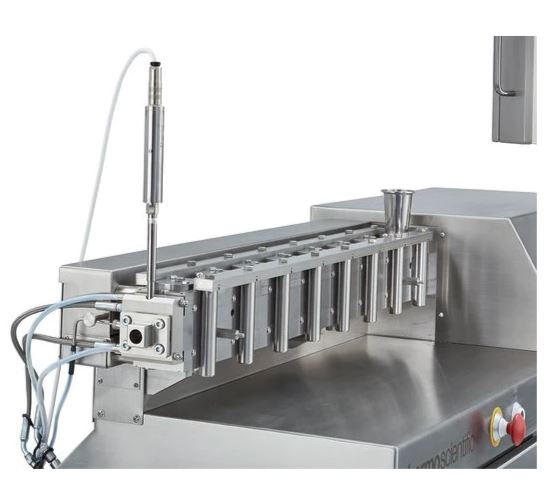
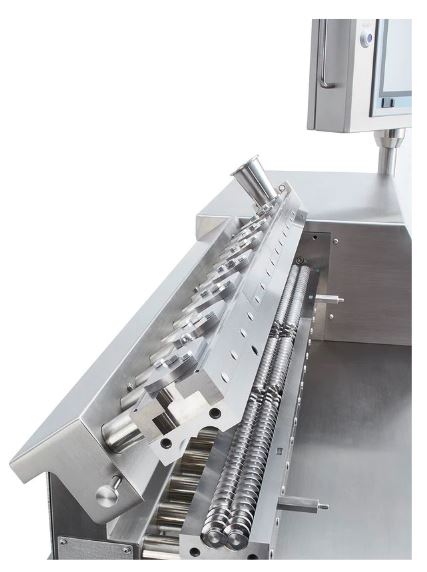
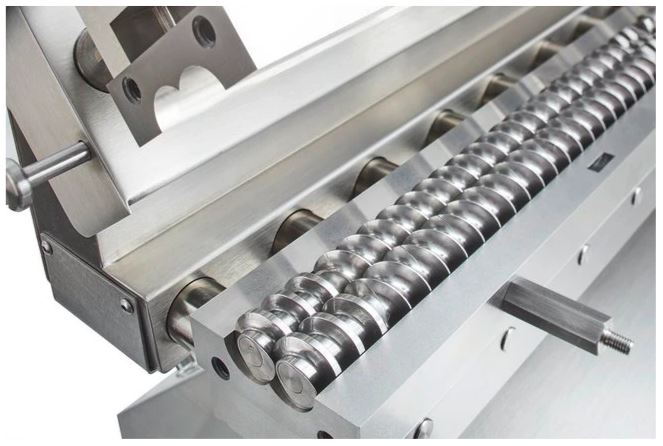
|
|
|
|
|
 |
Specification_Sheet_-_Pharma_mini_HME

|
|
Pharma mini HME Micro Compounder - The Thermo Scientific¢â Pharma mini HME is a GMP compliant conical micro compounder for Hot Melt Extrusion in research and development in the pharmaceutical industry. When developing new drugs, shortening time-to-market and reducing waste of expensive API's and overall development costs provide a distinct competitive advantage. Hence, quick and early assessment of new API/excipient formulations is critical. Hot melt extrusion and continuous processing can lead to speedier formulation development and cost efficient production. The Thermo Scientific Pharma mini HME allows users to identify the right drug candidates for hot melt extrusion by compounding as little as three grams of material.
With the Pharma mini HME, we offer a micro twin-screw compounder which requires as little as three grams of total material to identify the right drug candidates for hot melt extrusion. The compounder with conical co- or counter-rotating screws is designed to minimize waste and reduce downtime necessary for cleaning.
- Requires only 3g (4mL) of material for compounding
- Small footprint, fanless design with separate, touch-screen control for operation in fume cabinet or glovebox applications
- Removable and exchangeable product contact parts for quick and easy cleaning
- IP 54 for protection against dust and water allows the Pharma mini HME to be spray-washed
- Useable as small-scale production unit for throughputs of 100g/h
- Touch screen control with user levels and password protection
- Data logging software as option to record temperatures, torque, and screw speed
- Optional batch conversion kit to use the Pharma mini HME as small batch mixer
- Complementary workflow solution when coupled with the Thermo Scientific¢â HAAKE¢â MiniJet injection molder
Recommended for:
Materials:
- Pharmaceutical ingredients (API's)
- Excipients
- Medical polymers
- Drug delivery systems
- Soft gels
Applications:
- Hot melt extrusion
- Medical devices
- Implants
- Controlled drug release
- Handling and processing of highly potent API's in a glovebox
A small footprint reduces clean room volumes, and lower ingredient consumption reduces handling and operator exposure.
|
|
|
|
|
 |
Product_Specification_-_Pharma_mini_Implant_Line

|
|
Pharma mini Implant Line - Produce high-quality, injectable drug delivery systems with the Thermo Scientific¢â Pharma mini Implant Line. This automated end-to-end solution meets cGMP and FDA requirements. Accurate dosing of pre-blended material enters the extruder, which moves material through a die to produce a filament. A closed-loop filament control system ensures that the implant strand has minimal diameter variability. The strand is cut to the required implant diameter and length. Out-of-specification implants are automatically discarded, assuring 100% quality.
The Pharma mini Implant Line offers a complete solution for developing and producing injectable drug delivery systems. High-quality components and precise automation with integrated Quality Control and documentation assures consistent drug implant manufacturing.
Pharma mini Implant Line advantages
- Hermetically sealed material container for maximum operator and product safety
- High accuracy gravimetric feeding (¡¾ 0.5%, depending on material)
- Reproducible and stable extrusion process up to 100 g/h
- Accurate diameter control adjustable in the range of 0.5mm and 2.0mm; precision of final product is ¡¾ 0.005% to 0.05% (depending on - physical parameters of the compound used)
- Exact cutting of implant strand into specified length
- Automated sorting of in-spec and out-of-spec product for 100% quality assurance
- Integrated software control system for process monitoring, documentation and displaying all relevant system and process data
- 21 CFR part 11 compliant Batch Report and Audit Trail
Pharma mini Implant Line components
- Container with containment valve
- Gravimetric feeder with feeder screws and feeder stand
- Pharma mini HME micro compounder with co- or counter-rotating screws
- Filament diameter control and cutting unit with sorting unit
- PLC with integration of all Pharma mini implant line instruments
- Chiller unit
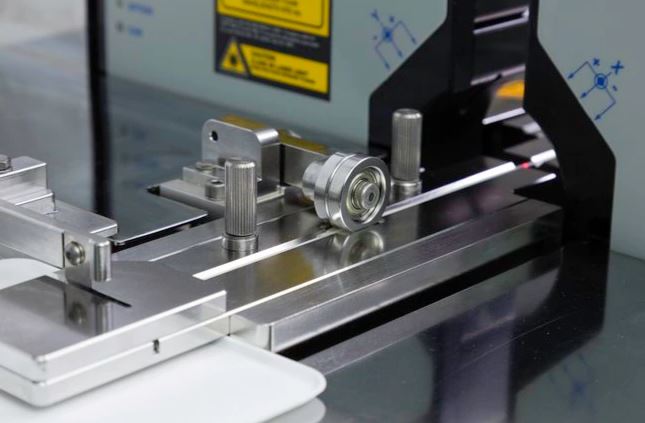
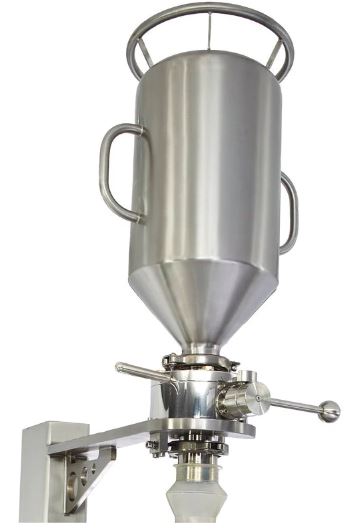
|
|
|
|
|
 |
Specification_Sheet_-_Pharma_mini_HME

Technical_Note_-_CailCut_Post-extrusion_System

|
|
Pharma mini HME Micro Compounder Accessories - Accessories for the Pharma miniHME Micro Compounder used for Hot Melt Extrusion in research and development in the pharmaceutical industry.
Thermo Scientific¢â CaliCut¢â Post-extrusion System highlights:
- Control precision: a 1D laser diameter gauge adjusts and pulls the strand enabling the diameter to be adjusted within set tolerances. A nominal strand diameter of 0.2 mm ~ 6 mm can be produced in conjunction with a nominal length of 1 mm ~ 200 mm.
Maximize flexibility: available with 350 mm, 700 mm or even 1200 mm belt lengths for cooling to meet a broad range of polymer formulation and throughput needs. Two different cutting mechanisms, a rotary and a linear cutting blade, optimize final implant sizing for a wide variety of implant materials. Make up to 600 cuts/minute.
Be 21 CFR part 11 compliant: stainless steel housing conforms to GMP guidelines while the software is used to control user access levels secures data export, and provide audit support. Documentation for IQ/OQ is provided.
|
|
|
|
|
 |
Specification Sheet: Phama mini Implant Line

Brochure: Pharmaceutical Extrusions and Analytical Solutions

Brochure: Twin-Screw Extrusions Solutions

Brochure: Application Compendium: Innovative Rheological and Extrusion Solutions for Drug Development

|
|
Drug Delivery Systems - Subcutaneous, solid implants are an emerging drug delivery system with special manufacturing needs when going from powder to ready-for-packaging product. In order to deliver the active pharmaceutical ingredient (API) safely and with a constant dissolution rate, a very homogeneous product with extremely tight tolerances in geometry is required. And when automating an implant manufacturing line, it becomes even more critical to assure consistent API/excipient compounding and to maintain precise quality specifications. Let us show you how.
Advantages of drug delivery systems
Subcutaneous implants or vaginal rings offer several advantages over solid oral dosage forms:
- The active pharmaceutical ingredient (API) can be released where it is needed most, reducing the required dose and helping reduce the drug's side effects
- The drug doesn't need to be administered as often, increasing the acceptance of new delivery systems
- Biodegradable materials can often be used in the manufacture of the delivery system, eliminating the need to remove implants
Pharma mini Implant Line
The Pharma mini Implant Line offers the opportunity to develop and manufacture implants in a fully automated and continuous process. This line uses a programmable logic controller (PLC) from material feed through to the final quality control of the implant size, including documentation such as batch report and audit trail.
A container with a containment valve for pre-blended material is connected to the gravimetric feeding system, enabling operator-safe handling and high accuracy in the feed rate. The Pharma mini HME Micro-Compounder produces a strand with a small diameter tolerance (¡¾0.005% to 0.05% depending on mechanical parameters of the compounds used). A laser sensor delivers data to control the strand diameter very precisely by adjusting the conveyor speed. Based on this data, the strand is cut to meet the length specifications of the implant. An automated sorting device assures that any out-of-specifications (OOS) implants are rejected and collected away from the in-spec implants.
CaliCut Post-extrusion System for implant production
As an accessory to our Pharma mini HME Micro-Compounder, we offer Thermo Scientific CaliCut Post-extrusion System to precisely calibrate polymer strands and cut them into well-defined implant devices.
As an accessory to the Pharma mini Extruder, this cutting system can be operated independently from the extruder control. It complements the extruder if fully automated production is not necessary or if the implant project is still in an R&D phase. The CaliCut System can produce 600 cuts/hour with variable lengths (1~200 mm) and diameters (0.2~6 mm). Its small footprint makes it an ideal addition to the Pharma mini HME Micro-Compounder.
Featured products for drug delivery system manufacturing
Pharma mini Implant Line
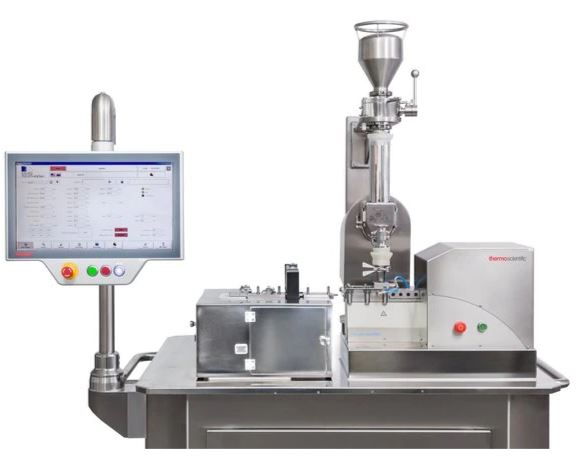
Pharma mini HME Micro-Compounder with cutting device
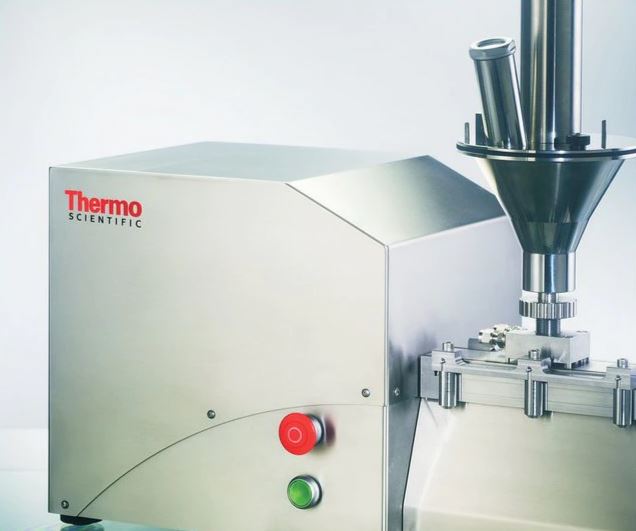
Pharma 16 extruder with cutting device
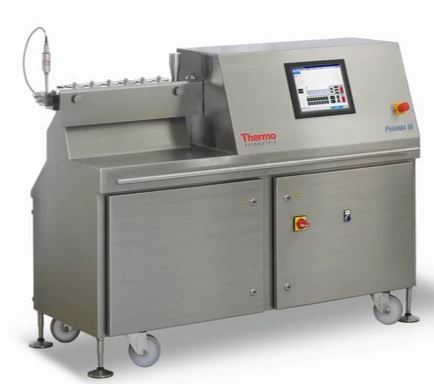
|
|
|
|
|
|
|
|
|
 |
Application Note: Evaluating Active Ingredients in Pharmaceutical Hot Melt Extrusion Products with Raman Imaging

Executive summary: Continuous Manufacturing of Pharmaceuticals: Scale-up of a Hot Melt Extrusion Process

Application Note: Investigating Process Parameter Mechanism for Successful Scale-up of a Hot Melt Extrusion Process

Scientific Poster: Investigating Decisive Parameters to Achieve Molecular Dispersion via Hot Melt Extrusion

Application Compendium: Innovative Rheological and Extrusion Solutions for Drug Development

Brochure: Twin-Screw Extrusion Solutions

|
|
Hot Melt Extrusion
Overcome drug formulation challenges
- Pharmaceutical manufacturers are using conical and twin-screw extruders to mix drug molecules with bioactive polymers in situations where drug ingredients are poorly soluble or unstable during processing. Extruders are also useful in preparing enteric dosages, sustained release dosages, in taste-masking, and to create forms such as films.
Why hot melt extrusion?
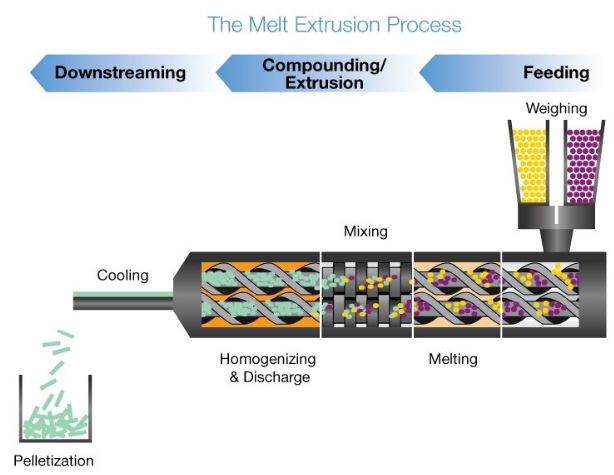
Hot melt extrusion (HME) is the processing of polymeric materials above their glass transition temperature (Tg) in order to effect molecular level mixing of thermoplastic binders and/or polymers and active compounds. Used in several industries, HME is a combination of melting and mechanical energy to improve continuous processing for reproducible analysis of materials, dust reduction and online monitoring.
In pharmaceutical manufacturing, HME is used to disperse APIs in a matrix at the molecular level, thus forming solid solutions. This enables drug delivery systems for poorly soluble drugs or specialized drug forms such as films for transdermal patches.
Watch our webinar series - Improving Solubility with Hot Melt Extrusion
Polymers
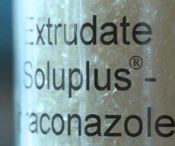
The choice of an adequate polymer as a matrix to form stable solid solutions is crucial in HME. Polymers with a high solubilization capacity are particularly suitable because they can dissolve large quantities of drugs. Polymers for hot melt extrusion experiments are based on different monomers and chemical structures, such as homopolymers, copolymers, amphiphilic copolymers as well as solubilizers and plasticizers. Consideration for each material must take into account the polymer's solubility in a solvent, which can vary from high lipophilicity to high hydrophilicity. A suitable solvent need to be selected for the preparation of solid solutions by spray drying, where polymer and drug must be dissolved in a volatile solvent.
Polymers for hot-melt extrusion must exhibit thermoplastic characteristics and must be thermally stable at the proper extrusion temperature. In developing an HME drug system, the glass transition and melting temperatures are critical factors. The extrudability of a polymer is mainly determined by Tg or Tm and melt viscosity. Most polymers demonstrate thixotropic behavior where the viscosity reduces as a function of increasing shear stress.
Active pharmaceutical ingredients
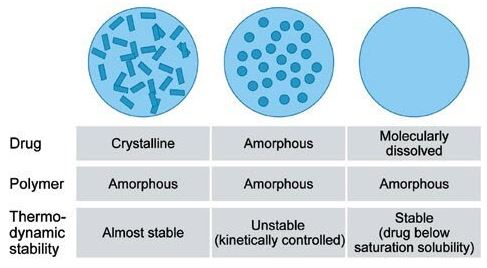
Present drug discovery methodology produces candidate drugs of increasing molecular size and lipophilicity, which results in poor solubility and permeability. Less than 10% of new drug candidates demonstrate both high solubility and permeability, and 30~40% of the drugs that appear on the World Health Organization Essential Drug List were reported to be poorly water-soluble or lipophilic. HME disperses the drug in the matrix at a molecular level by forming a solid solution.
HME is available for a number of applications, including amorphous solid dispersion, controlled release systems, polymorph generation, novel cocrystallisation (solvent-free continuous cocrystallisation), porous polymeric systems and Process Analytical Technology (PAT).
Watch webinar - Employing Hot Melt Extrusion As a Cost Effective Method of Increasing Solubility Of Water Insoluble APIs
Processing parameters
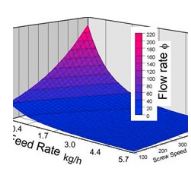
In the hot melt extrusion process, the API and the excipients are fed into the extruder. All components are sheared, heated, plastified, mixed and dispersed, and finally shaped by pressing them through a die opening. Developing a HME manufacturing project requires control of several processing parameters that affect residence time distribution, and specific mechanical energy consumption (SMEC) must be considered such as temperature of the melt at the extruder die, pressure at the die, and torque.
See Investigating Decisive Parameters to Achieve Molecular Dispersion via HME (poster).
Featured products for drug delivery system manufacturing
Pharma mini HME Micro Compounder
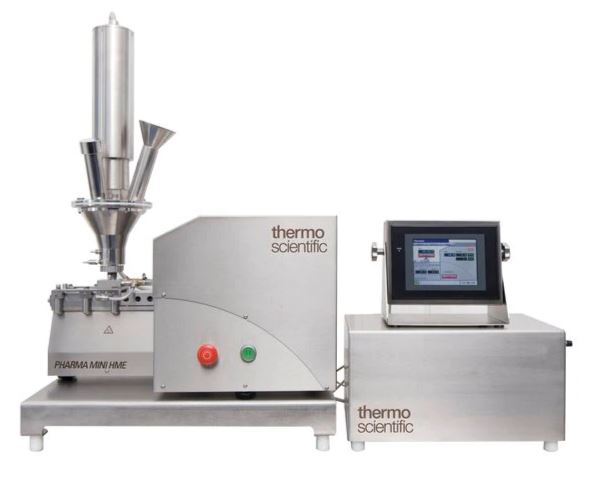
Pharma 11 Twin-Screw Extruder
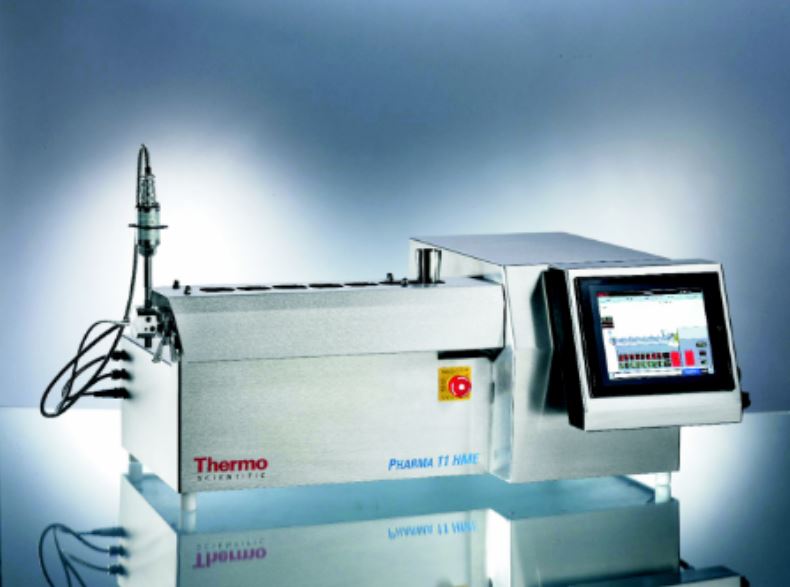
Pharma 16 Twin-Screw Extruder
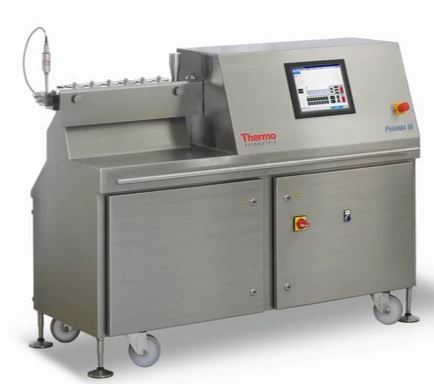
|
|
|
|
|
|
|
|
|
 |
Brochure: Twin-Screw Extruders

|
|
Extrusion and Mixing Solutions for Cosmetic and Personal Care Products
- Color cosmetics are a fast-growing market, and rapid development of new, innovative products offers a distinctive advantage. That¡¯s where tools for continuous processing can make a big difference.
Easily tailor your mixing process and meet compliance requirements
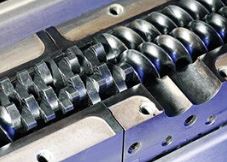
Individual and configurable screw elements help design mixing properties tailored to your process by alternating mixing zones followed by rest zones. It is possible within one process to have vigorous mixing to disperse agglomerates of one ingredient, for example, and then gentle mixing at a later stage of the process, for example with pearls.
Our twin-screw extruders are fully GMP compliant, helping you meet regulatory demands around the globe. All processing parameters are electronically recorded and available for documentation and submission to regulatory agencies. Benchtop and production size instrumentation is available to fulfill all requirements in the development and manufacturing process.
Pharma 16 Twin-Screw Extruder
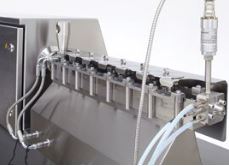
Rapidly develop cosmetic formulations and adopt continuous processing methods using the Thermo Scientific Pharma 16 Twin-Screw Extruder. Optimize process development parameters with less time and effort than batch processes and easily scale-up to larger Thermo Scientific extruders with minimal amounts of expensive ingredients.
Pharma 11 Twin-Screw Extruder
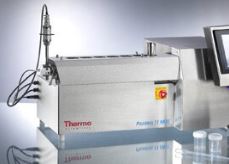
Perform material- and labor-effective extrusion with the Thermo Scientific Pharma 11 Twin-Screw Extruder. It requires only a small amount of expensive ingredients. This continuously operating twin-screw extruder can help reduce development time for both powder and semi-solid forms of eye makeup.
Color cosmetics ~ faster, better, more profitable!
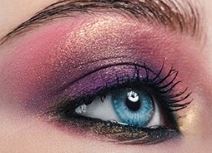
Eye shadow. Mascara. Blush. Consumers want the latest colors in their makeup, so it pays to develop new products more quickly and efficiently. See how mixing via twin-screw extrusion in a continuous process reduces development steps and yields a more consistent and homogeneous end product.
|
|
|
|
|
|
|
|
|
 |
|
|
|
|
Brochure: Pharmacuetical Extrusion and Analytical Solutions

Brochure: Twin-Screw Extrusion Solutions

Application Note: Dry Granulation as a Twin-Screw Process in Pharmaceutical Applications

Product Specifications: HAAKE RheoWin Software 21 CFR Part 11 Tools

Poster: Twin-Screw Granulation ~ a Systematic Analysis of Process Parameters

Poster: Continuous Twin-Screw Granulation: Analysis of Process Parameters and Scale-Up

Flyer: Security and Compliance in Pharma with XRD

Application Compendium: Innovative Rheological and Extrusion Solutions for Drug Development

Brochure: Safely Accelerating Drug Development for Brighter Outcomes

Application Note: A Fast HPAE-PAD Method for Determination of Carbohydrates and Glycols in Pharmaceutical Formulations

|
|
Drug Formulation and Manufacturing
Solutions for scale-up and continuous processing
- Addressing challenges in pharmaceuticals where API solubility and processing stability, taste-masking, enterics, and specialized dosage forms are critical projects, Thermo Scientific extruders and related analytical instrumentation provide the shortest path from feasibility studies to production in drug formulation and manufacturing.
Compounding and extrusion technologies have been used in manufacturing for centuries and have become a valuable tool in creating novel drug formulations, and in the transition from inefficient batch processing to continuous manufacturing.
Featured drug formulation and manufacturing technologies
Hot Melt Extrusion
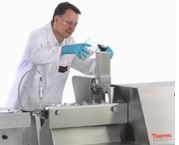
Melt extrusion has been used in the plastics and polymers industry for decades. Advances in formulation enable poorly soluble drug molecules to be incorporated into solid dispersions using a polymeric carrier. Hot melt extrusion is an alternative to wet agglomeration, a good carrier for sustained release forms and taste-masked dosages. Extrusion processes can also create films for oral strips or dermal patches in a solvent-free process.
Drug Delivery Systems
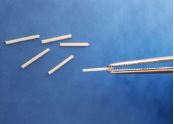
Hot melt extrusion (HME) is a key technology that can produce alternative drug delivery systems such as subcutaneous, solid implants for controlled-release treatment in ophthamology and cancer (e.g., hormone) as well as extrusion of biocompatible or biodegradable polymer/drug formulations.
HME can be configured to create a fully-automated implant production line with small tolerances in diameter and length. This continuous manufacturing process is an ideal solution, offering high-precision control of implant dimensions, a small footprint for full containment and simple cleaning for aseptic requirements of FDA approved materials.
Continuous Granulation
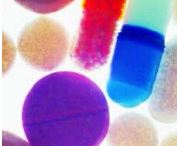
According to the US FDA, the continuous manufacturing process reduces human errors caused by starts and stops during the batch process. Continuous granulation is also safer and more reliable. In a continuous process, ingredients are fed and mixtures sent to downstream production. Extruders have been used in wet granulation processes for many years; twin-screw extruders are now playing a central role in pharmaceutical manufacturing.
Analytical Instrumentation
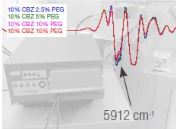
Rheometry and spectroscopy play important roles in developing and implementing extruder-centered drug formulations. The use of near infrared (NIR) spectroscopy for the analysis of active ingredients in pharmaceutical formulations is well known. The technique is nondestructive, has excellent signal-to-noise ratios and can use fiber optics to take sampling to the process. NIR spectroscopy is an ideal choice to monitor the output of a hot melt extruder. Complementary to NIR in bulk and in-line sampling, Raman spectroscopy adds microscopic imaging to analyze tablet homogeneity and the analysis of co-extrusions.
ODFs made easy with HME
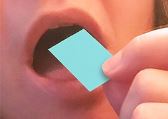
Orally disintegrating films (ODFs) allow safe, easy and exact dosage of active pharmaceutical ingredients (APIs). They also improve bioavailability of the API and help avoid the first pass effect. Hot-melt extrusion (HME) works well for manufacturing ODFs; it¡¯s well-established, provides reproducible results, and doesn¡¯t require solvents. Produce high-quality ODFs at lab- or production-scale.
Hints to optimize pharma processes via continuous granulation
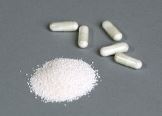
The switch from batch processing to continuous manufacturing of pharmaceuticals can really pay off with efficiencies and other savings. But how to set up a successful new continuous process - that's a challenge for everyone. We teamed up with Innopharma Technology to help.
Unique Advantages of Process Analytical Technology in Twin-Screw Granulation describes an experiment combining Thermo Scientific Twin-Screw Granulation (TSG) technology and Innopharma Process Analytical Technology (PAT). Read the results to learn which extruder parameters to adjust for the most impact on the continuous granulation process.
Improve pharma and biotech manufacturing processes and help ensure patient safety
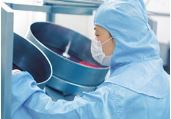
Save time, improve processes, protect brand integrity, and ensure patient safety, from raw material identification through the pharmaceutical manufacturing process, to finished and packaged pharmaceutical product inspection.
Lab ideas for medicine makers ~ current topics for pharma ~ biopharma analytical labs!
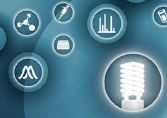
Lab ideas for people ~ like yourself in analytical labs making medicines, directed by topics, ideas and thoughts from your fellow medicine makers. Each month, a new theme addresses challenges and solutions around technology and workflows.
|
|
|
|
|
|
|
|
|
 |
|
|
Scale-Up and Pilot Projects for Hot Melt Extrusion
Identify the right drug candidates
- Thermo Scientific twin-screw extruders are built with similar geometries. This enables experimentation and feasibility projects with a lab-scale (11 mm screw) extruder that minimizes the use of expensive APIs and enables easy clean-up between experiments.
Micro-compounder finds drug candidates
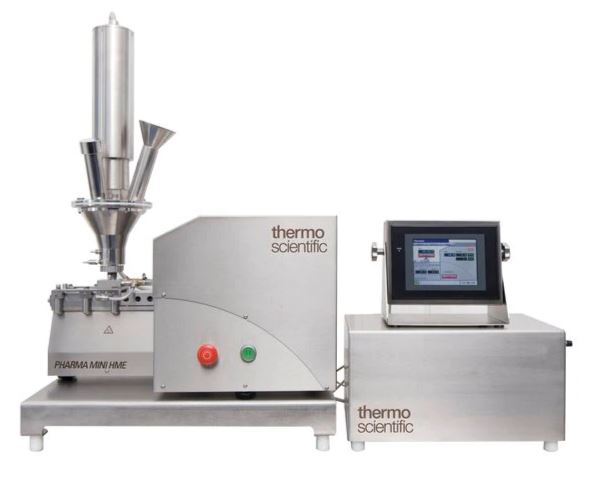
Finding the right API/excipients formulation and testing if this formulation is the right candidate for hot melt extrusion can be difficult. A micro twin-screw compounder requires as little as 3 grams of total material to identify the right drug candidates for hot melt extrusion. The compounder with conical co- or counter-rotating screws is designed to minimize waste and reduce downtime necessary for cleaning.
Benchtop extruder for research and small-scale production
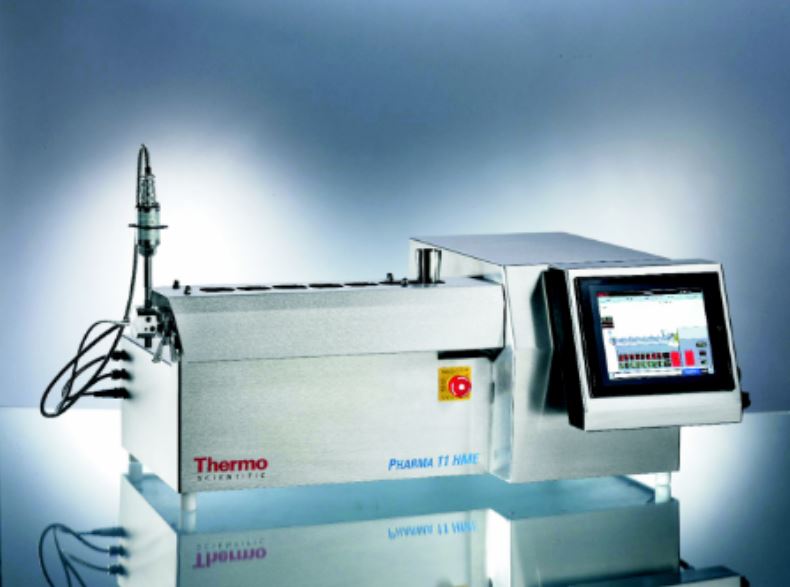
With a minimum throughput of 20 g/h, a benchtop extruder is ideal for Phase 1 research applications, especially when developing and testing recipes with expensive API and associated compounds. As a GMP-compliant unit, the Thermo Scientific Pharma 11 is also suitable for clinical trials and small-scale production for throughputs up to 2.5 kg/h. The screw and barrel designs are geometrically scalable across the whole Thermo Scientific portfolio of extruders from lab and pilot through to production scale.
Formulation development platform
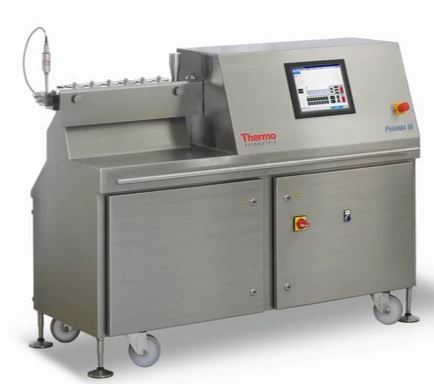
Designed to fit between the development lab and production line, a modular 16 mm twin screw extruder is capable of managing several drug formulation projects, including controlled release formulations, solubility enhancement, co-extrusion and implants, abuse deterrent formulations, and wet and melt granulation projects. A modular design enables formulation scientists to switch from hot melt extrusion and continuous granulation projects without engineering the extruder system.
Twin-screw granulation
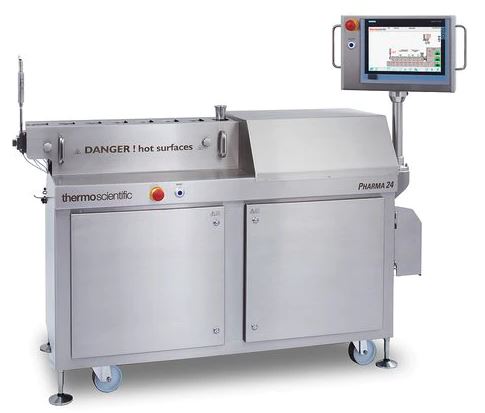
Reduce scale-up risks by running production on same equipment as development. A 24 mm twin-screw granulator will match the performance of 300 to 600 litre batch processors. Reduce in-process inventory to minimize risks to expensive ingredients and from ATEX hazards. Maximum volume of ingredients in the process is approximately 100 ml for 16 mm and 360 ml for 24 mm twin screw granulators.
Production-scale HME
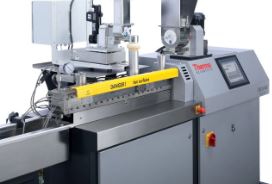
For consistent, controllable processing of hot melt drug formulations that are suitable for PAT, the 24mm twin screw extruder promises reduced product changeover time, minimized scale-up risk and easy cleaning.
This platform includes a number of integrated ancillary equipment for both project development and small-scale production including pre-mixers, feeders, chill rolls, air-cooled conveyors, pelletizers, and cast sheet or blown film lines. GMP standard pharmaceutical versions of the ancillaries are available with stainless steel construction and dust-tight touch-screen operator interface.
|
|
|
|
|
|
|
|
|
 |
|
|
|
|
Application Note: Dry Granulation as a Twin-screw Process in Pharmaceutical Applications

Unique Advantages of Process Analytical Technology in Twin-Screw Granulation

Brochure: Pharmaceutical Extrusion and Analytical Solutions

Brochure: Twin-Screw Extrusion Solutions

Brochure: Continuous Granulation for Drug Development

Application Compendium: Innovative Rheological and Extrusion Solutions for Drug Development

|
|
Continuous Granulation
- Continuous granulation offers many opportunities to overcome the challenges of traditional batch production of tablets and capsules. It¡¯s efficient, inherently scalable and has advanced to a point of true reliability and flexibility. It can also be implemented all at once, or a little at a time. Consider the many ways below that twin-screw granulation can help you boost your oral drug formulation processes.
Continuous granulation ~ the future of oral drug manufacturing
Most oral drugs are available as tablets and capsules because it¡¯s easy to store and consume medicine in this form. Traditionally pharmaceutical manufacturers have created such oral dosage forms in batches. Now, many are considering a continuous manufacturing process. Why? How?
Why continuous granulation?
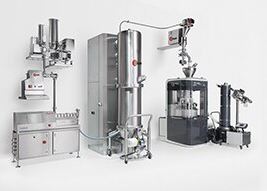
Small, medium and large batches of pharmaceuticals are prone to variations and expensive delays:
- Manual steps invite human error
- Transportation from one step to the next may cause material segregation
- Time-consuming disassemby and cleaning delay production
- Production scale-up requires bigger, more expensive equipment
Continuous manufacturing reduces/eliminates the issues above and makes subsequent tableting easier. With online monitoring, continuous manufacturing also enables drugs to be released as soon as they¡¯re manufactured ~ there¡¯s no waiting on analytical results before products can ship.
Today, continuous manufacturing is no longer an ¡°untested¡± process. Companies have gained experience and proven that it can be successfully implemented with a significant positive impact.
HME can be configured to create a fully-automated implant production line with small tolerances in diameter and length. This continuous manufacturing process is an ideal solution, offering high-precision control of implant dimensions, a small footprint for full containment and simple cleaning for aseptic requirements of FDA approved materials.
Set up continuous manufacturing so it really works!
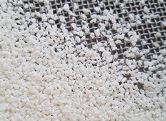
Establishing a successful continuous twin-screw granulation (TSG) process can be tricky. Download this free whitepaper with expert advice for process design, development and scale-up for pharmaceuticals. The paper even includes information about how the parameters of twin-screw extruders can impact scale-up of a continuous process.
Batch Processing ~ it¡¯s OK to let go
It can seem daunting move away from batch processing which has served pharmaceutical manufacturers well for so many years. Many questions arise when looking at a new process:
- Will I lose flexibility for producing multiple products?
- How will I characterize the homogeneity of my mix?
Flexibility. There is great flexibility in continuous manufacturing. Switching production from one drug product to another is possible with quick, easy replacement of product contact parts to eliminate the risk of cross-contamination. And modularity allows the granulator to be easily set up for a different product¡¯s required process steps.
Characterizing homogeneity: Online analytical technologies (e.g., near-infrared or NIR spectroscopy) allow manufacturers to characterize homogeneity and other material properties at any time in the process. So the ability to characterize properties is maintained in continuous manufacturing via online analyzers.
How to implement continuous granulation?
Quantum leap vs Slow migration¡¦
The pharmaceutical manufacturing process can be continuously operated from mixing of initial powders to packaging of final tablets. This can be done with a twin screw extruder and subsequent drying in a fluidized bed system.
So the starting point can be small a stand-alone twin-screw granulator. If more granules are needed, simply run the instrument continuously for a longer period of time.
Modules can be added along the way, expanding the parts of the process that operate continuously:
- Dosing systems
- Dryers
- Tablet presses
- Etc.
A full continuous system can be grown module by module, or be put into place all at once with an entire processing line installation. Such installations often take place by scale-out or scale-up.
Scale-out: creating other small copycat systems in different locations or simply run the process on one instrument scale for a longer time period
Scale-up: transferring the process to high volume, high speed production systems
Thermo Scientific pharmaceutical twin-screw extruders are designed to bring you the benefits of continuous manufacturing whatever your pace may be.
We offer 11 mm, 16 mm and 24 mm pharmaceutical extruders that can stand alone or be partially or fully integrated into your manufacturing process. Systems are available for dual twin-screw granulation (TSG) or hot melt extrusion (HME) processes, or for dedicated TSG. Modules expand their use throughout the process from raw materials to tableting.
|
|
|
|
|
|
|
|
|
 |
|
|
|
|
|
|



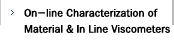
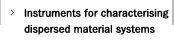
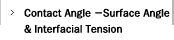


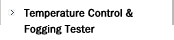



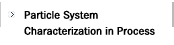



|