 |
 |
 |
 |
 |
|
|
 |
|
 |
|
|
|
|
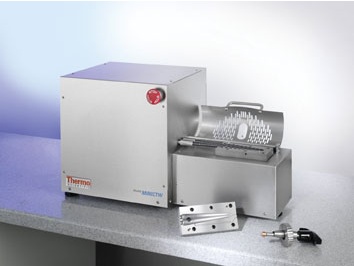 |
|
|
|
|
|
|
|
|
|
 |
|
|
|
|
|
 |
|
|
|
|
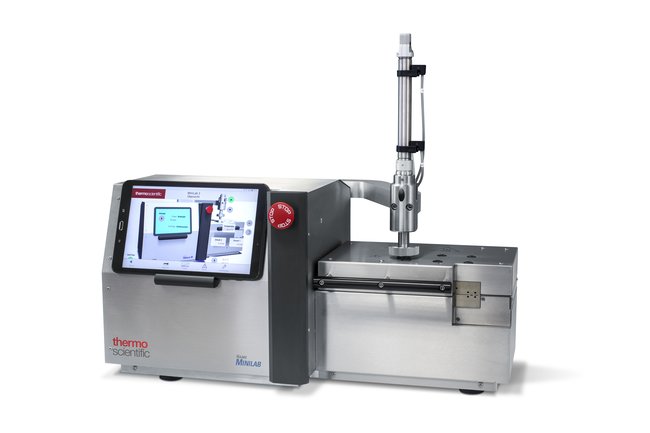 |
|
Micro Rheology
Compounder |
|
Find unmatched flexibility in designing today's products for tomorrow's world. The Thermo Scientific¢â HAAKE¢â MiniLab 3 Micro Compounder provides extrusion specifications and online rheology measurements for pilot and scale-up projects across a range of compounded materials.
Using material amounts as small as 5 grams, or 7 cm3, the HAAKE MiniLab 3 delivers meaningful results that enable you to streamline your new material development. Its screw speed and pressure range make it ideal for compounding expensive materials and for performing reactive extrusions. |
Getting new compounds faster and documenting structural changes online has never been easier. The HAAKE MiniLab 3 Micro Compounder is a conical, twin-screw compounder with an integrated backflow channel. The compounder works as either a stand-alone unit or can be fully computer-controlled system, and can be used with either co- or counter-rotating screws. It is equipped with an inert gas flush system. Due to its channel and a bypass valve design, the residence time is well defined. Two pressure transducers are integrated in the backflow channel, which allow the measurement of relative melt viscosity when counter-rotating screws are used. Using the optional force feeder with the HAAKE MiniLab 3 Micro Compounder, continuous extrusion with very small volume flows is possible.
|
|
|
The HAAKE MiniLab 3 Micro Compounder Features: |
|
|
 |
Co- and counter-rotating twin screws |
|
|
 |
Integrated viscosity measurement (with HAAKE PolySoft OS) |
|
|
 |
Automatic bypass operation for circulation/extrusion |
|
|
 |
Pneumatic feeding |
|
|
 |
Local control via tablet (Android¢â) for intuitive operation |
|
|
 |
Split barrel exit for easy cleaning |
|
|
 |
Compact enough to fit into laboratory fume hood |
|
|
|
|
|
|
|
|
|
|
 |
|
|
|
|
|
 |
|
|
|
|
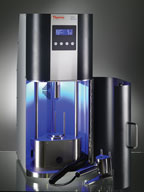 |
|
HAAKE MiniJet Piston Injection Molding System |
|
The MiniJet is a piston injection moulding machine and provides efficient sample preparation for testing mechanical and measuring rheological properties.
A variety of different sample specimen forms is commonly required to perform thorough mechanical testing. These specimens can be produced using an injection moulding machine, cut manually from pressed sample plates, or created manually using some type of specific sample test device. The need to produce various sample forms coupled with the common reality of limited material quantities can often create great difficulty in a product's development. |
|
|
The HAAKE MiniJet system allows you to optimise your development process and realise cost reduction opportunities: |
|
|
 |
The production of test specimens from as little as 5g of material |
|
|
 |
Test specimens can be produced from various forms of material - powders, pellets, or melts |
|
|
 |
A control and design concept that provides simplistic handling with consistent, reproducible results |
|
|
 |
Specimen geometries offered from standard to unique, customised forms |
|
 |
 |
|
Injection pressure : max. 1,200 bar
Dimensions : 300mm x 460mm x 710mm
Power : 230V +/- 10%, 3.15 A, 50/60 Hz; 110V +/- 10%, 3.15 A, 60 Hz
Air Pressure : max. 10 bar
Mould temperature : max. 250degC
Cylinder temperature : max. 400degC |
|
|
|
|
|
|
|
|
|
 |
|
|
|
|
|
 |
|
|
|
|
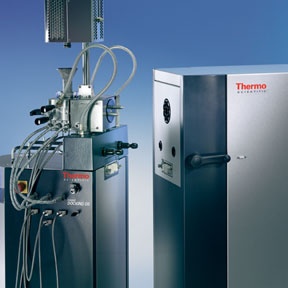 |
|
HAAKE PolyLab OS Torque Rheometer |
|
The HAAKE PolyLab OS is a modular torque rheometer platform for process engineering applications. The "OS" stands for the fundamental platform concept - that of Open System, allowing a number of standardised sensors and systems to be connected to if for otical, viscosity, and spectroscopy measurements.
The HAAKE PolyLab OS is designed to conduct mechanical characterisation of fluids or solids through deformation, shear or stress at defined environmental conditions.
The new HAAKE PolyLab Open System (OS) is an innovative torque rheometer platform designed to optimize process engineering applications. Data for melt characteristics, dynamic viscosity under shear load and the effectiveness of additives, heat and shear stability are readily attainable with his system.
The core technology is based on an open industry standard, allowing sensors and systems to be connected for optical, viscosity and spectroscopy measurements.
The modular HAAKE PolyLab can be quickly and easily adapted to the requirements o a specific application. This is enabled by a standardised CAN Open Bus for internal communication and a USB interface for connection to a PC. |
|
|
Application areas include:
|
|
|
 |
Polymers - Processing related data such as melt characteristics, the effects of additives, temperature and shear stability as well as dynamic viscosity during shear are of great importance to the development of innovative polymers. Process simulation in the form of compounding and extrusion of rods, profiles or films combined with rheological or visual measurements, assists in optimising procedural parameters to create samples for testing. These samples can also be used to conduct checks on incoming and outgoing goods for viscosity, dispersion or plastifying characteristics. |
|
|
 |
Rubber - The impact of carbon black on the cross-linking characteristics of a rubber compound and the dispersion, vulcanisation and flow properties of rubber are key to product quality in the rubber industry. Optimising the end product mixing times is important to ensure efficient use of production plants, and also to successfully launch competitive products into the market. |
|
|
 |
Ceramics - Rheological measurement data relating to dispersability, ability to withstand injection moulding and flow characteristics of ceramic injection moulding compounds and pastes provide the ceramics industry with information to optimise products. |
|
|
 |
Specimen geometries offered from standard to unique, customised forms |
|
|
|
|
|
|
|
|
 |
|
|
|
|
|
 |
|
|
|
|
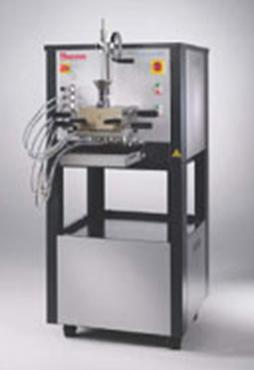 |
|
QC ¹× R&D ÀÛ¾÷¿¡ »ç¿ë °¡´ÉÇÑ °æÁ¦ÀûÀÎ Torque Rheometer. Àû¿ëÀÌ °¡´ÉÇÑ ÂøÅ»½Ä ¸ðµâ ¹æ½ÄÀ¸·Î ´Ù¾çÇÑ Lab Scale Single/Conical Twin Screw Extruder ¹× ¹Í¼ µîÀÌ Á¦°øµÈ´Ù. |
|
|
More IQ for your QC - benefit from the difference! |
|
|
 |
Concept
- Modular torque rheometer with
interchangeable mixer, single_screw
extruder, conical twin_screw extruder
- bench or floor model
- Control via HAAKE PolySoft software |
|
|
 |
Backwards Compatibility
- Hardware compatible with old mixers,extruders
- Existing accessories can still be used
- Data compatibility (importing of old data) |
|
|
 |
Interfaces/Communication
- CAN open control communication with temperature, motor controller
- CAN open data communication for pressure and remote signals
- USB interface to host computer (LAN as option) |
|
|
|
|
|
|
|
|
|
|
 |
|
|
|
|
|
 |
|
|
|
|
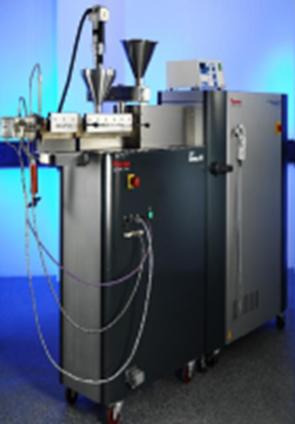 |
|
HAAKE PolyLab OS º»Ã¼¿¡ ÀåÂøµÇ´Â 16mm ¹× 24mm Screw
Daimeter ÀÇ µîÃà Æ®À© ÄÄÆÄ¿î´õ ¸ðµâ. ½ºÅ©·ù ¼¼±×¸ÕÆ® ¹è¿ÀÌ
ÀÚÀ¯·Î¿î Split Barrel Çü½Ä. Parallel Twin Screw Extruders
The new Thermo Scientific Rheomex
PTW 24 MC (Modular Compounder)
is a modular twin-screw extruder
module for the lab extruder and
mixer platform HAAKE PolyLab OS.
Twin-screw lab extruders have a
proven record in continuous com-
pounding with feed-dosing of different
additives (liquid or solid) along the
extruder barrel. The combination
of a twin-screw extruder unit with
additional sensors offers the ability
to measure material properties of the
melt during processing. |
|
|
|
|
|
|
|
 |
|
|
|
|
|
 |
|
|
|
|
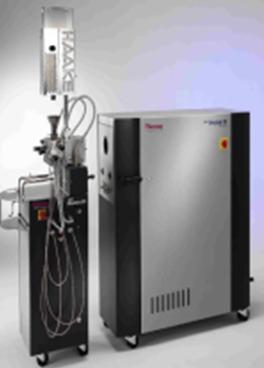 |
|
High shear ¿¡¼µµ Torque ÀÇ Èçµé¸²ÀÌ ÀüÇô ¾ø´Â Round feeding section ÀÌ ÀåÂøµÈ 500C ±îÁö heating ÀÌ °¡´ÉÇÑ 120cc¹× 625cc è¹ö°¡ ÀåÂøµÈ µÎ°¡Áö ¸ðµ¨ÀÌ ÀÖÀ¸¸ç ¿°æÈ¼º ¹× ¿°¡¼Ò¼º ¸ðµ¨ÀÌ ¼±Åà °¡´É. |
|
|
|
|
|
|
|
 |
|
|
|
|
|
 |
|
|
|
|
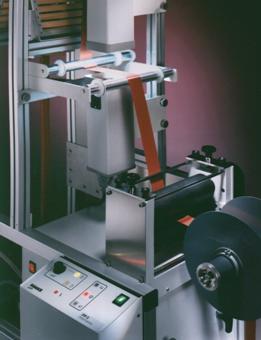 |
|
HAAKE PolyLab ¾ÐÃâ±â ¹× OQT¸¦ ÀÌ¿ëÇÑ Fish-Eyes
¹× Black-SpotsÀÇ Differentiation ¿¡ »ç¿ëµÇ´Â Built-in CCD
Ä«¸Þ¶ó¿Í Image Analysis ¼ÒÇÁÆ®¿þ¾î¸¦ »ç¿ëÇÑ Film QCÀåÄ¡. |
|
|
|
|
|
|
|
 |
|
|
|
|
|
 |
|
|
|
|
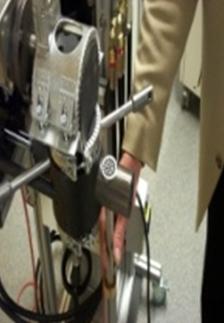 |
|
°íºÐÀÚ Composites ³»ºÎ ÀÔÀÚÀÇ ºÐ»êµµ ÃøÁ¤¿ë
Hydraulic Screen Changer (Filtering and Sieving
½ÃÇè¿ë) / Mixer ³»ºÎÀÇ Àü±â Àüµµµµ ÃøÁ¤À» ÅëÇÑ
ºÐ»êµµ ºÐ¼® / ´Ù¾çÇÑ Dies (Rod, Capillary,
Wire-Coating, PVCÀü¿ë, Tubing, Fiber Spinning,
Elongation µî) ¹× Die Swell ÃøÁ¤±â µî |
|
|
|
|
|
|
|
 |
|
 |



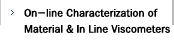
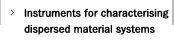
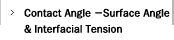


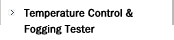



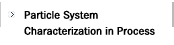




|